- Home
- Contents
- Technical Documents
Technical Documents
This is P&R Technology’s two-component liquid meter mix dispenser
Technic article
Two-component liquid meter mix dispenser
PR-2D MODEL
The precise metering and mixing of the two-component resins (epoxy, silicone, urethane, etc.) composed of the main agent/curing agent in a mixing ratio of 100:100 to 100:5 within the ±1 to 3% deviation range using a precision transfer pump is possible. In particular, it is possible to cope with the raw materials’ recent high viscosity and high filler components.
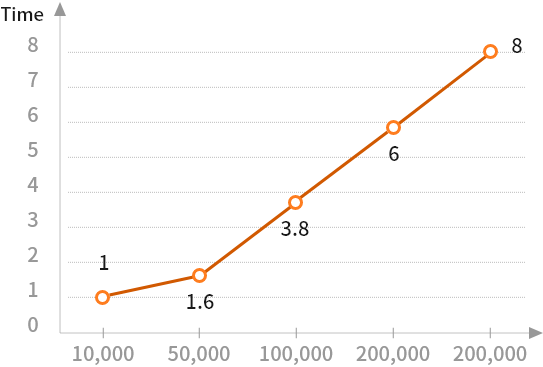
Defoaming time before an improvement according to the raw material viscosity
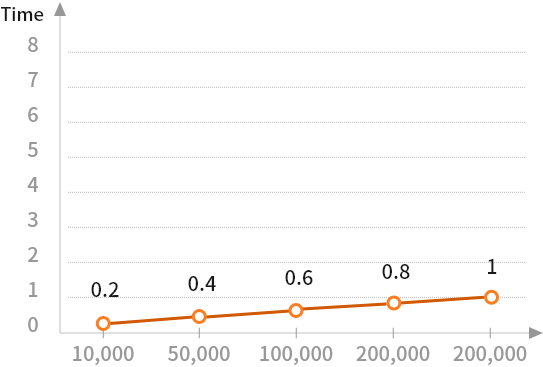
Defoaming time after an improvement according to the raw material viscosity
* The graph above may vary depending on the specific gravity and type of the raw material, and the higher the viscosity of the raw material, the shorter the defoaming time.
Advantages and Differentiation
Minimize the mixing ratio deviation within ±1 ~ 3% by using a pump according to the characteristics of raw materials (viscosity, specific gravity, etc.) (use gear pump, piston pump, mono pump)
Mixing ratio range
100:100 ~ 100:5
Dispense the Volume Range
Minimum of 1cc or more (Technical consultation is required for less than 1cc)
Compatible with high-viscosity / high-filler raw materials
Prevent sedimentation by using a circulation pump, and use a mono pump or a piston pump in case of pump wear
Reduced vacuum defoaming time
Using a vacuum accumulator (a device that can store raw materials in the middle) makes vacuum defoaming possible even during the discharge operation without a separate vacuum defoaming process.
Classification according to the raw material viscosity | Before enhancements | After enhancements |
---|---|---|
Vacuum defoaming time for a typical low-viscosity raw material | 1 hour | After the initial 10 to 30 minutes of raw material circulation, vacuum degassing and the discharging of the tank are possible simultaneously. |
Vacuum defoaming time for a mid/high-viscosity raw material | 1 hour or more – up to 8 hours (depending on the raw material) |
Core Technology
The two-component liquid meter dispenser is configured to maintain the vacuum defoaming for the perfect mixing of raw materials, correct mixing ratio, and discharge weight.
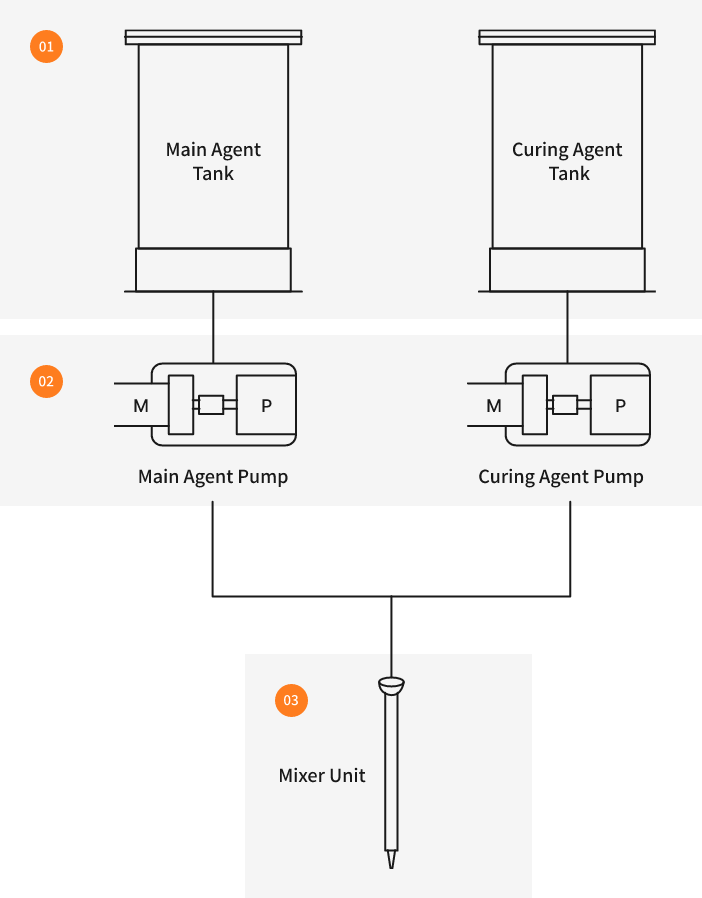
Tank/line preheating device : automatic temperature control
Tank agitator : prevent sedimentation
Tank vacuum defoaming device : removing the air bubbles
Precision transfer pump
- Gear Pump : Low/medium viscosity non-filler type
- Mono pump/piston pump :
- ① For the medium/high viscosity
- ② FILLER TYPE
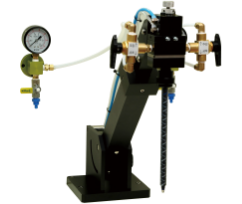
Static Mixer
(Stationary Mixer)
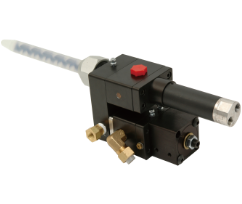
Dynamic Mixer
(Rotational Mixer)
Product name | Urethane for electronics |
---|---|
Viscosity (Mpa.s at 23℃) | 70 / 500 |
Specific gravity (at 23℃) | 1.19 / 0.97 |
Ratio (weight ratio) | 53 / 100 |
SHOT “1” | Part A (g) | Part B (g) | Ratio (%) |
---|---|---|---|
1 shot | 35.200 | 66.300 | 53.092 |
2 shots | 35.200 | 66.300 | 53.092 |
3 shots | 35.100 | 66.400 | 53.861 |
4 shots | 35.100 | 66.400 | 53.861 |
5 shots | 35.100 | 66.400 | 53.861 |
Average | 35.140 | 66.360 | 52.954 |
Maximum | 35.200 | 66.400 | 53.092 |
Minimum | 35.100 | 66.300 | 52.861 |
* The above graph may vary depending on the specific gravity and type of the raw material, and the higher the viscosity of the raw material, the shorter the defoaming time.